Welcome to Foshan Pinshang Machinery Co, Ltd.
Service Hotline:
+86 13791266555
29
2024
-
09
How to Handle Ink Foaming in Corrugated Box Printing
Category:
The water-based printing of corrugated cardboard has gained widespread popularity in the packaging industry due to its environmental friendliness and safety. However, ink foaming remains a persistent challenge that can significantly impact print quality and reduce production efficiency. This article will delve into the causes of ink foaming and provide comprehensive solutions to help you produce high-quality prints.
Root Causes of Ink Foaming
Ink foaming can be attributed to a variety of factors. In addition to the ink formulation itself and the printing environment, the operating condition of the printing equipment plays a crucial role. For instance, excessive machine speed can trap air in the ink, leading to foaming; issues with the diaphragm pump, such as uneven ink suction or excessive air pressure, can also increase the air content in the ink. Furthermore, the quality of the paper, printing pressure, the condition of ink rollers and plates, and the operator's experience all influence ink foaming.
Comprehensive Solutions
To address ink foaming, we can take the following measures:
- Optimize Ink Formulation:
- Rigorously control pigment dispersion to ensure fine and uniform pigment particles.
- Select resins and additives with good compatibility to enhance ink stability.
- Adjust the type and dosage of defoamers according to specific conditions.
- Improve Printing Process:
- Optimize ink circulation system: Regularly clean the ink circulation system to maintain smooth ink flow and prevent impurities.
- Maintain ink rollers: Regularly inspect ink rollers for wear and replace worn rollers promptly.
- Manage plates: Select high-quality plates and maintain them regularly.
- Adjust printing pressure: Adjust printing pressure according to the characteristics of the paper and ink.
- Control Printing Environment:
- Temperature control: Maintain a stable temperature in the workshop to avoid excessive heat or cold.
- Humidity control: Control the humidity in the workshop to avoid excessive humidity or dryness, which can affect ink drying.
- Ventilation: Ensure good air circulation in the workshop to reduce the amount of impurities in the air.
- Strengthen Equipment Maintenance:
- Regular maintenance: Regularly maintain printing equipment to ensure stable operation.
- Troubleshooting: Promptly identify and troubleshoot equipment failures to prevent ink foaming caused by equipment malfunctions.
- Select High-Quality Paper:
- Choose paper with good flatness, moderate water absorption, and stable surface tension.
- Strengthen Personnel Training:
- Provide systematic training to printing operators to improve their operational skills and troubleshooting capabilities.
Additional Suggestions for Producing High-Quality Prints
- Introduce intelligent systems: Utilize intelligent equipment and systems to monitor various parameters in the printing process in real-time, enabling timely detection and resolution of issues.
- Establish standardized operating procedures: Develop detailed standardized operating procedures to ensure that every step of the process is carried out according to specifications.
- Strengthen quality control: Establish a comprehensive quality control system to conduct rigorous inspections of printed products and ensure product quality.
Conclusion
While ink foaming can be a complex issue, it can be effectively addressed by taking a comprehensive approach. By optimizing ink formulations, improving printing processes, controlling the printing environment, strengthening equipment maintenance, and selecting high-quality paper, we can significantly reduce ink foaming and produce high-quality prints.
Related News

Service TEL:
+86 13791266555

Add:
No. 61B, Anhua Road, Fuwan Town, Hecheng Street, Gaoming District, Foshan City, Guangdong Province, China
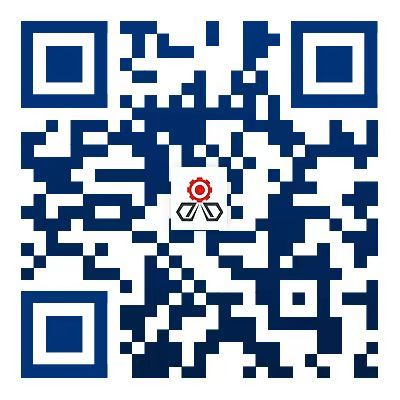